6 interesting facts about sandblasting you probably didn’t know
1. Sandblasting was invented in the United-States in 1870
Sandblasting was invented in 1870 by an American soldier named Benjamin Chew Tilgham.
After observing the etching effect of wind-blown sand on the glass panes of windows, Tilgham had the idea of exploiting this phenomenon and using it in industrial processes.
His patent for sandblasting was registered in the USA around 1870, followed by a British patent later the same year.
Tilgham went on to receive numerous accolades for his invention, including the Grand Medal of Honor from the City of New York and the Elliot Cresson Medal from the Franklin Institute.
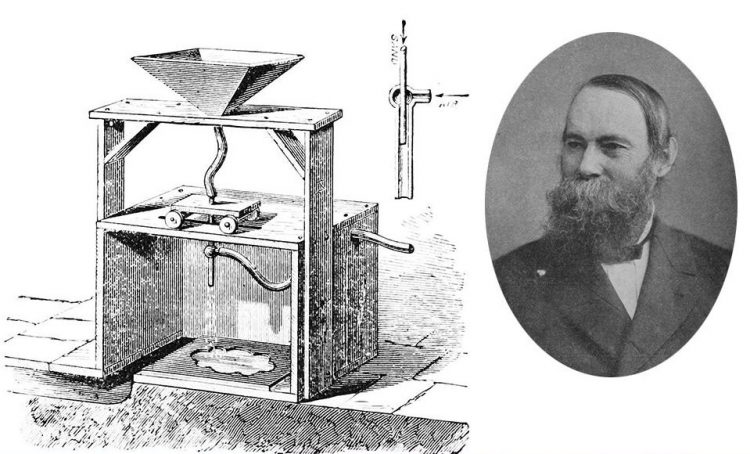
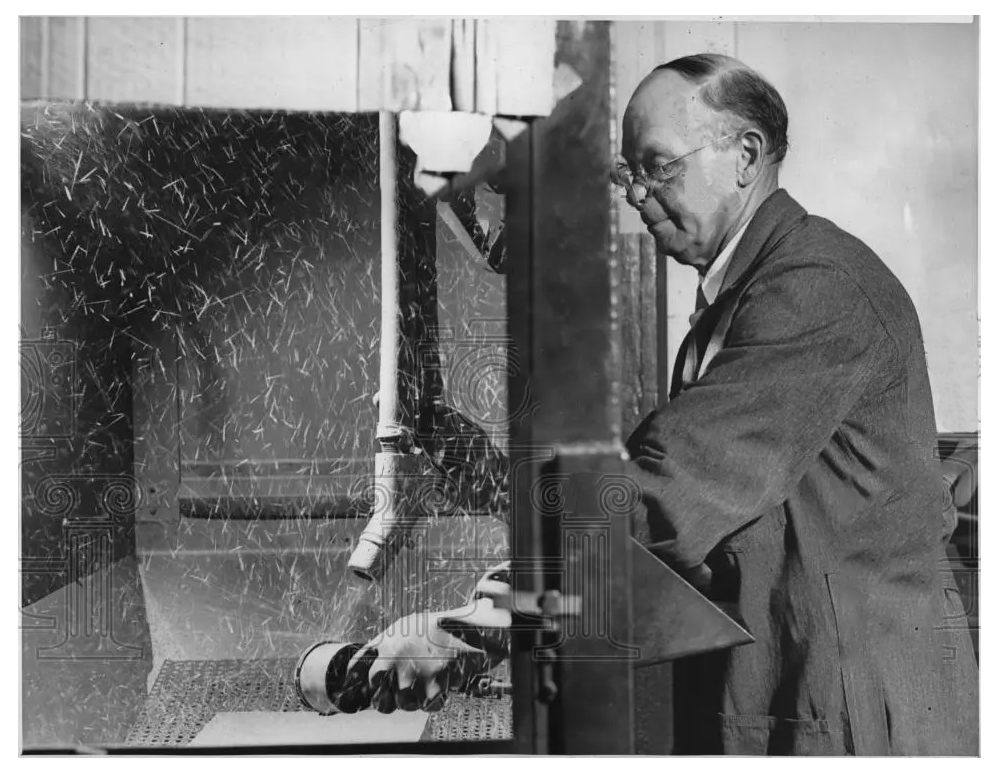
2. The first sandblasting cabinet was invented in 1918
The first sandblasting cabinet was invented in 1918.
The first sandblasting cabinet consisted of a viewing screen, a turntable and an extraction fan to remove the dust.
The cabinet was created to facilitate the blasting process, make it more efficient and try to protect workers from the dust particles produced.
Originally, sandblasting was carried out using silica sand. The dust produced by this process was often inhaled by workers, causing a lung condition known as silicosis.
3. Great Britain was the first country to ban sandblasting using silica sand in 1950.
Because of the high risk of silicosis among workers and the difficulty of controlling exposure, the use of crystalline silica in abrasive blasting operations was banned in Great Britain in 1950 and in other European countries in 1966.
In 1974, OSHA recommended that silica sand (or other substances containing more than 1% free silica) be banned as an abrasive blasting material, and that less hazardous materials be used in blasting operations.
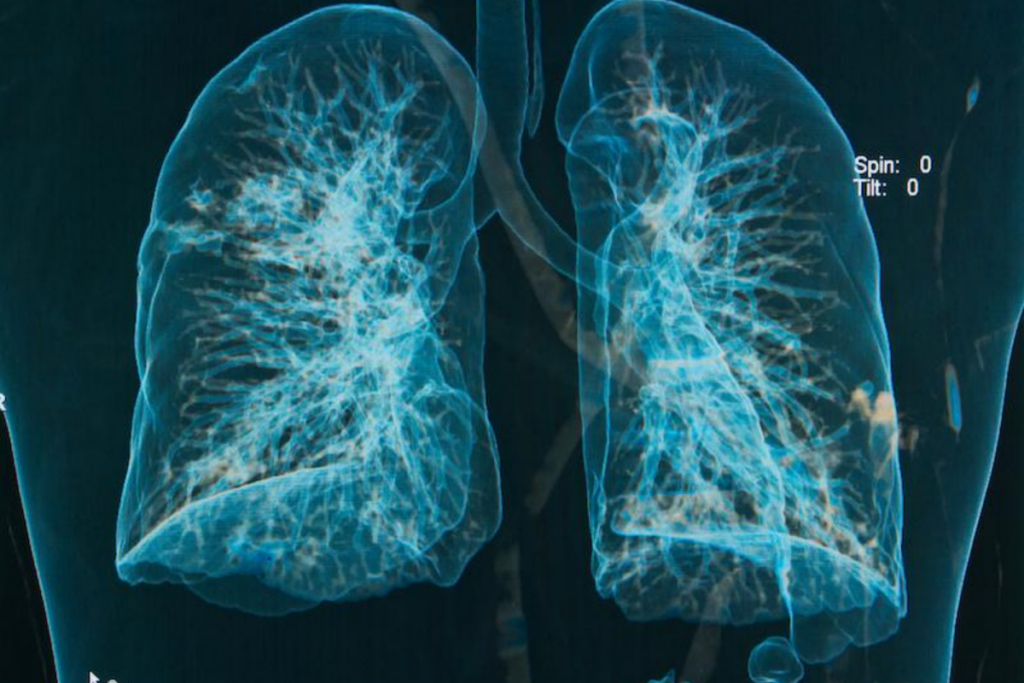
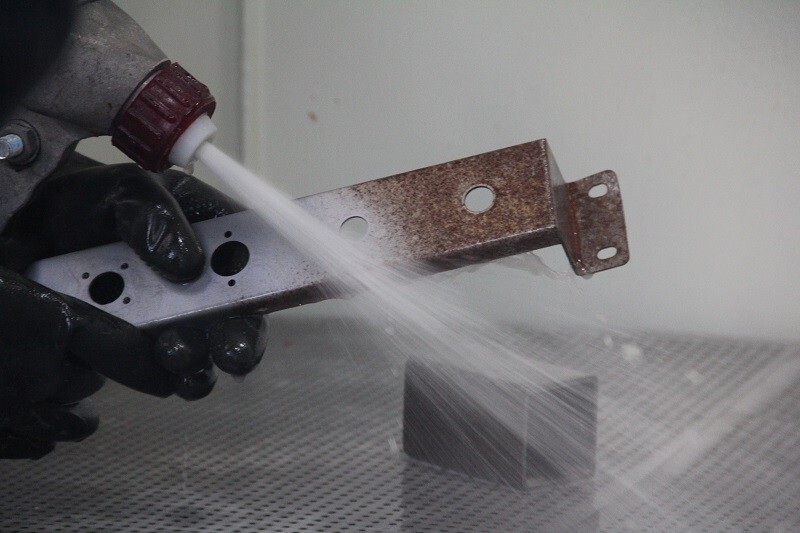
4. The first wet-blast machines were developed in the late 1940s.
It took almost 80 years after the first sandblasting machine was invented for the first wet sandblasting machine/process to see the light of day. Wet blasting follows much the same process as standard sandblasting, but uses a mixture of abrasive with a liquid such as water, instead of a dry abrasive.
The main advantages of wet sandblasting are dust reduction, and the elimination of the risks associated with the static electricity produced by traditional sandblasting.
The main disadvantages of wet sandblasting are water consumption, higher cost than traditional sandblasting and oxidation (rusting) of ferrous metals.
5. The market for blast abrasives was estimated at 30,175,200 tons in 2022.
The market for blast abrasives worldwide is extremely large and growing.
Global Market Insights, a market research firm, has estimated the abrasives market at 60,350,400,000 lbs (60 billion?!) or 30,175,200 tons per year, representing expenditure of around US $9,000,000,000.
What’s even more impressive is that this market is expected to grow at a compound annual growth rate of 7% over the next seven years.
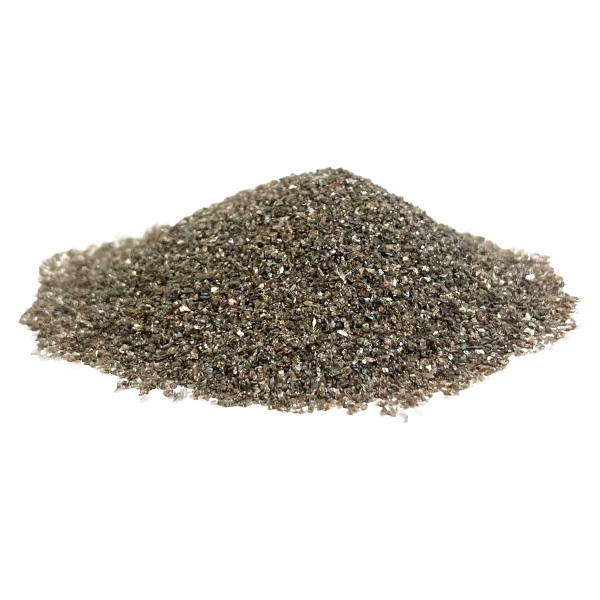
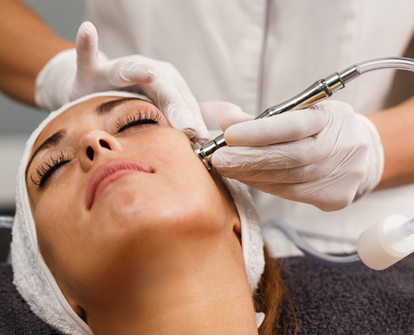
6. Sandblasting is used for much more than just surface preparation
Many industries have integrated sandblasting technology into their operations. Some of the most interesting include
Dentistry: In dentistry, abrasive blasting is used to improve dental hygiene by cleaning and removing plaque and sediment. It can also be used for color correction, as well as to eliminate tooth decay, as an alternative to traditional drilling.
Aesthetics: Microdermabrasion is essentially sandblasting for the skin. Aestheticians use an instrument that sprays a micro-abrasive onto the skin, smoothing it and removing imperfections.
Glass art: Sandblasting is often used for artistic engraving in glassmaking. Engraving with sandblasting is used to create images or patterns on glass products, and gives a frosted appearance to treated surfaces.
Medicine: Some medical products, such as stents, are created using a micro-fabrication process that can leave microscopic burrs and other impurities. These impurities need to be removed to avoid adverse reactions in the human body. Stent manufacturers therefore use micro-abrasive sandblasting to solve this problem.