Abrasive Media for Sandblasting: A Comprehensive Guide
Sandblasting, a powerful and versatile surface preparation technique, has become indispensable across numerous industries. Sandblasting is most often used for surface preparation, cleaning, and finishing tasks.
Whether you’re restoring an antique car, cleaning a ship’s hull, or preparing a metal surface for a fresh coat of paint, choosing the right abrasive media is the key to a successful sandblasting project. In this comprehensive guide, we will navigate the intricacies of abrasive media, exploring different types of blast media, factors to consider when selecting the most suitable one for your needs, and how to estimate the quantity needed for your specific project.

Which factors should you consider When Selecting Abrasive Media
The choice of abrasive media is a critical decision that can significantly impact the outcome of your sandblasting project.
The choice of abrasive to use depends on several factors and may not always be straightforward.
Here are some key factors to keep in mind when making your selection:
Material Being Blasted
Different materials require different abrasive media. The abrasive blast media you should use for your project will depend on the material’s hardness, sensitivity, as well as the desired outcome. Common materials include metals (steel, aluminum, stainless steel), wood, plastic, rubber, composites, and concrete.
Metals: For metals like steel or aluminum, common abrasive media options include steel grit, aluminum oxide, or garnet.
Wood: Soft woods, like pine or cedar, require a gentle abrasive media like plastic abrasive or walnut shells to avoid damaging the wood. Hard woods, like oak or teak, can withstand more aggressive media like aluminum oxide, Jetmag, glass beads etc.
Concrete: Concrete surfaces can be blasted with abrasives like garnet, crushed glass, or silicon carbide, depending on the depth of surface profiling required.
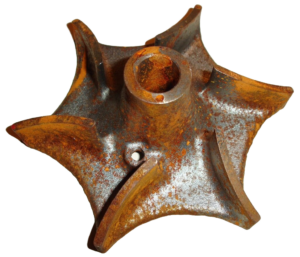
Desired Surface Finish
The type of finish you want to achieve will also have an impact on your choice of abrasive media. If the blasting is an early step in a multi-step process, the surface finish of the material after blasting may be less important than if the blasting is a later or final step. Some processes will allow for sanding, or other surface finishing as a subsequent step. In these cases, a coarser or larger media can be used, as the surface finish right after blasting is less of an issue.
Coarse Finish: If you need to remove heavy rust or paint quickly, abrasive media like steel grit or aluminum oxide with larger grit sizes will be more effective.
Smooth Finish: For a smoother, polished surface, consider finer abrasive media such as glass beads or plastic beads.
Equipment on hand
Unless you are planning to purchase new sandblasting equipment, the equipment you have on hand or available to you, will play a big role in determining which abrasive to use for your project.
Abrasive media comes in various forms, such as grit, shot, or beads, and your equipment should be designed to handle your chosen media effectively.
The owner’s manual for your sandblasting equipment will be an indispensable guide when choosing between different types of abrasive media. Should you not have access to your owner’s manual, you should contact the equipment manufacturer.
Cost
When evaluating the total cost of abrasives for your project, there are two factors that should be considered: the cost of the product but also the efficiency of the chosen abrasive material. Balancing these two factors is crucial for optimizing project costs and success.
Product Cost: The overall cost of abrasive media includes the initial purchase cost as well as the final disposal or recycling expenses. While some media may be more expensive upfront, its longevity and effectiveness can make it the most cost-effective in the long run.
Efficiency: Assess the cutting rate (the rate at which abrasive media removes material) and wear rate (the durability of the media) to determine efficiency. Greater efficiency can lower labor costs, which are often a significant portion of the total project costs.
Environmental Concerns
Environmental factors are increasingly important when selecting which type abrasive media to use. The environmental considerations can be both internal and external, such as restrictions based on the specific work location as well as any local laws and regulations that are in place.
For example, a sandblasting project adjacent to a river, will have different considerations than a sandblasting project done in a large, well-ventilated industrial space.
Recyclability: Some media, like steel shot, steel grit, and aluminum oxide, can be re-used or recycled multiple times, reducing waste, and greatly lowering costs.
Dust and Containment: Dust generation can be a concern when sandblasting. If you are working indoors, with subpar ventilation, you should consider dustless blasting options.
Laws and regulations: Local laws and regulations may limit the types of abrasives that can be used, specifically near waterways or other sensitive environments.
What are the different types of abrasive media?
Abrasive media comes in a diverse array of types and sizes, each with its own unique properties and applications.
Selecting the right type of blast media for your project is a crucial step to get optimal results.
Some of the most commonly used types of abrasive media in sand blasting include:
Steel Shot
Steel shot abrasive is made of small spherical steel particles of various sizes. Steel shot has a uniform structure, providing optimal resilience and resistance to fatigue. Its high durability and resistance to impact fatigue provide high cleaning efficiency at the most economical cost.
Due to its properties, Steel Shot has high recyclability, meaning it can be used many times over, keeping blast media purchasing costs lower over time.
Steel shot blasting abrasive media is available in a range of different hardness grades, and mesh sizes. Like all steel media, ferrous contamination, or rust, against the blast surface will occur.
Blasting with steel shot produces very low levels of dust and airborne particles.
Steel Grit
Steel grit abrasive media shares many of the same properties as steel shot.
The main difference between steel shot and steel grit is the shape of the pellets. Steel shot has a spherical, uniform shape while steel grit is randomly shaped, with angular edges.
Like steel shot, steel grit abrasive blast media is highly recyclable, and can be re-used many times, however the sharp, angular edges of the product will start to gradually round over time with repeated uses.
Steel grit is also available in different hardness grades and mesh sizes.
Plastic Blasting Media
Plastic abrasive media is a much less aggressive media than most other abrasives.
Due to its low hardness, only 3-4 on the Mohs hardness scale, it is ideal for blasting softer materials such as fiberglass, aluminum, copper, brass, plastics, rubber, composites, and electronic components. It is also well-suited for applications where the goal is to minimize any etching of the final surface.
Additionally, due to its non-metallic nature, plastic blast media does not generate any heat when working with metal substrates, eliminating the risk of warping.
Plastic abrasive blasting media is silica free and leaves no residual deposits on the blasted surface.
However, plastic media is more prone to static electricity. Therefore, extra care must be applied to ensure that all blasting equipment is properly grounded.
Glass Beads
Glass beads are another commonly used type of abrasive media. Glass beads are available in various mesh sizes, depending on the application.
Glass beads are a less aggressive blast media choice and are most suitable for the blasting of softer substrates such as soft metals like brass and aluminum, or plastic and die-cast surfaces.
Glass Bead abrasives are usually produced from melting recycled glass, making them an environmentally friendly choice. Glass beads can typically be re-used many times, further increasing its environmental benefits, while also keeping costs low.
Although crushed glass abrasive media may contain some silica, glass beads abrasive media doesn’t, as the production process eliminates the silica from the material.
Blasting with glass beads produces no airborne silica, eliminating any health concerns for the operator.
Glass beads are also chemically inert, making them a top choice for industrial applications.
JetMag®
JetMag® is a synthetic sand made of olivine and pyroxene widely used for blast cleaning.
It offers excellent sanding quality, and its cost/performance ratio is highly competitive. It allows for either faster cleaning and/or reduced abrasive consumption.
JETMAG® is completely non-toxic, contains no heavy metals, and no toxic elements. It is not listed as a hazardous material under the WMHIS system, making final disposal relatively easy. The use of this abrasive also generates very little dust, making it safe for the operator, and the environment.
JETMAG® is a preferred choice for applications requiring fast cleaning action at low cost. However, it is moderately friable which means it shatters upon impact, resulting in lower recyclability when compared to other synthetic abrasives.
Jetmag can be used on ferrous and non-ferrous metal substrates and will not leave any oxidation.
JETMAG® has very low density, which means a higher volume of media for a given weight.
JETMAG® is available in different mesh sizes ranging from as little as 0.5mm to 6mm.
Aluminum Oxide
Aluminum Oxide is among the hardest blast abrasives available. It is also a top choice for applications that must avoid contamination or corrosion.
Aluminum oxide can be used to blast many different substrates including metal, glass, and wood, and is mainly used for etching and finishing. Blasting with aluminum oxide provides excellent cutting power and typically leaves a clean, textured surface.
Aluminum oxide produces low dust, and has 0 detectable silica, making it a very safe option for the operator.
Aluminum Oxide is a low-iron content abrasive, meaning it will not leave any rust on the surface of your parts eliminating any possible problems in subsequent future processes.
Aluminum oxide is recyclable and reusable, lowering the total cost of use.
Aluminum oxide particles have an angular shape and are available in many different mesh sizes.
Its high density and angular sharpness, make it highly versatile and is suitable for use in both wet and dry blasting processes.
GMA Garnet
Garnet is widely used, natural, mined, mineral based abrasive.
Garnet is recognized for its high cleaning efficiency, meaning it requires less abrasive for the same job when compared to other abrasive materials. It also has a relatively low cost per square meter.
Garnet can be used in both wet and dry blasting applications, including water cutting. Sandblasting using garnet produces very little dust, which makes it ideal for use in environmentally sensitive applications or in confined spaces.
One of the unique properties of Garnet is its crystalline structure, which cause the material to fracture into sharp-edged grains. This property
Walnut Shells
Walnut shells are commonly employed as an abrasive media in sandblasting for various applications. Their natural hardness, which falls within the Mohs hardness scale of 2.5 to 4, makes them suitable for delicate surfaces and softer materials like wood, plastics, and fiberglass, where more aggressive abrasives might cause damage. They are also used to blast metal surfaces, where any scoring or etching is unacceptable, such as blasting the interior cylinder walls of an engine.
The rounded and irregular shape of walnut shells ensures a gentle but effective abrasive action that removes contaminants, coatings, and rust without gouging or pitting the underlying substrate.One significant advantage of using walnut shells is their environmental friendliness, as they are biodegradable and non-toxic, making cleanup and disposal incredibly easy.
However, walnut shells may not be as efficient for heavy-duty tasks or on harder materials compared to harder abrasives like aluminum oxide or steel shot.
Additionally, they can generate dust during the blasting process, which requires appropriate dust control measures for operator safety and workspace cleanliness. Therefore, the choice of walnut shells as an abrasive media should consider the specific requirements of the task as well as the materials involved.
Quick Reference Abrasive Media Guide
Ceramic Shot | Glass Bead | Stainless Cut Wire | Steel Shot | Steel Grit | Aluminum Oxide | Crushed Glass | Garnet | Jet Mag | Silicon Carbide | Plastic Media | |
Finishing | ✓ | ✓ | ✓ | ✓ | ✓ | ✓ | ✓ | ✓ | ✓ | ✓ | X |
Cleaning / Removal | ✓ | ✓ | ✓ | ✓ | ✓ | ✓ | ✓ | ✓ | ✓ | ✓ | ✓ |
Peening | ✓ | ✓ | ✓ | ✓ | X | X | X | X | X | X | X |
Surface Profiling (etching) | X | X | ✓ | X | ✓ | ✓ | ✓ | ✓ | ✓ | ✓ | ✓ |
Working Speed | Med | Med | Med | Med | Med-High | High | High | High | Low-High | Very High | Med-High |
Recyclability | High | High-Low | High | Very High | Very High | Med-High | Med-Low | Med | Low-High | Med-Low | Med |
Probability of metal removal | Very Low | Very Low | Very Low | Very Low | Med-High | Med-High | Low-Med | Med | Med-High | Med-High | Very Low |
Hardness (Mohs scale) | 7 | 5.5 | 6-7.5 | 6-7.5 | 8-9 | 8-9 | 5.5 | 8 | 7-7.5 | 9 | 3-4 |
Bulk Density (lb/cu.ft) | 150 | 100 | 280 | 280 | 230 | 125 | 100 | 130 | 85 | 96 | 46-60 |
Mesh Size | 8-46 | 30-440 | 20-62 | 8-200 | 10-325 | 12-325 | 30-400 | 16-325 | 16-60 | 36-220 | 18-80 |
Typical Blast Pressure (psi) | 30-90 | 30-80 | 30-90 | 30-90 | 30-90 | 30-90 | 30-50 | 30-80 | 50-100 | 30-80 | 30-50 |
How much abrasive media will I need for my project?
Estimating the quantity of abrasive media required for your project is important to avoid unnecessary expenses and delays. To calculate the amount needed, consider the following factors:
Surface Area: Calculate the total surface area to be blasted (in square feet or square meters).
Blast Profile: Determine the desired surface profile depth (measured in mils or micrometers).
Media Consumption Rate: Consult with your abrasive media supplier to obtain the media consumption rate per unit of surface area and profile depth for the specific media you’ve chosen.
Using these values, you can calculate the required abrasive media quantity as follows:
Abrasive Media (lbs)=Surface Area (sq ft)×Profile Depth (mils)×Media Consumption Rate (lbs/sq ft/mils)
By considering these factors and performing the calculation, you can ensure that you have an adequate supply of abrasive media for your sandblasting project.
Conclusion
Selecting the right abrasive media for your sandblasting project is a crucial decision that requires careful consideration of various factors.
By assessing the material, desired finish, environmental concerns, cost and efficiency, safety, and equipment compatibility, you can make an informed choice.
IST Surface Technologies offers a wide range of abrasive media options and expert guidance to ensure your sandblasting projects achieve optimal results.
Contact us today to explore our comprehensive selection of abrasive media and receive personalized assistance for your specific applications.
Still not sure which abrasive is best for your use-case? Get in touch with an expert by sending us an e-mail to info@istsurface.com or giving us a call at 1-877-629-8202